QC7つ道具とは?覚え方から使用例まで分かりやすく解説
投稿日:2022/5/11
製造業において、品質管理(QC:Quality Control)の徹底は、会社の信頼を保つためや顧客満足度を維持するために重要です。しかし、日常の生産活動の中でいろいろな要因から不具合は発生してしまいます。
そのような不具合情報を見える化し改善に活かすために「QC7つ道具」が使用されます。この記事では、QC7つ道具の概要や製造現場で起きがちな問題に対してどのツールを使用すれば効果的な対策を考えることができるのかを分かりやすく説明しています。
- 【目次】
- 1. QC7つ道具とは
- 1.1. QC7つ道具の覚え方
- 2. QC7つ道具の活用事例
- ①パレート図
- ②ヒストグラム
- ③散布図
- ④特性要因図
- ⑤チェックシート
- ⑥グラフ
- ⑦管理図
- 3. まとめ
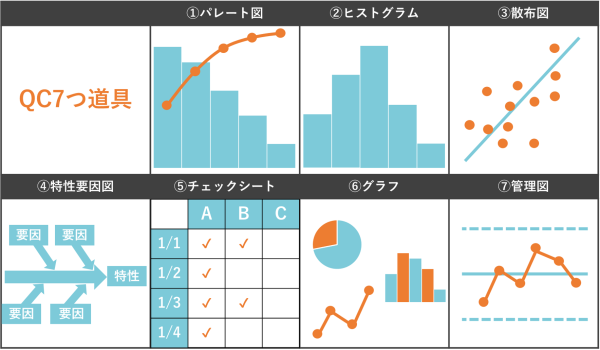
1. QC7つ道具とは
QC7つ道具とは、日々の生産活動の中で蓄積される様々なデータを整理、分析することで、品質改善に活用するための代表的な分析ツールのことです。QC7つ道具を活用すれば、主に数値データを図表化できるため、問題点がどこにあるのか視覚的に分かるようになります。具体的にQC7つ道具とは以下を指します。
これらのツールを主に以下のような目的に対して使い分けることで、収集したデータを活用できます。
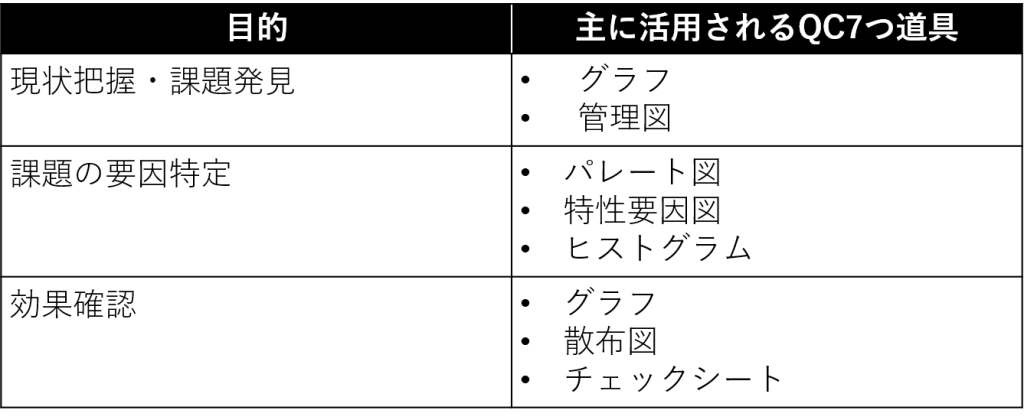
※言語データを図や表で視覚的にまとめる道具群「新QC7つ道具」についてはこちら
1.1. QC7つ道具の覚え方
QC7つ道具の覚え方として良く知られているのは「サンチェ監督引っ張れそう」の語呂に合わせて覚える方法です。
- サン:散布図
- チェ:チェックシート
- 監 :管理図
- 督 :特性要因図
- 引っ:ヒストグラム
- パレ:パレート図
- そう:層別・グラフ
なお、ここでは先ほど紹介したQC7つ道具には無い「層別」という項目を追加しています。QC7つ道具に層別を含む・含まないという双方の考え方があるためです。
層別とは、特定の基準に沿ってデータを分けることを指します。例えば、作業員別であれば「男女別・年齢別・身長別」、時間別であれば「週別・日別・週別」というふうにデータを分けることです。
2章では、それぞれのツールについて具体的に説明していきます。
2. QC7つ道具の活用事例
ここでは、各道具の説明と具体的な活用シーン、そして使用にあたっての注意点について解説します。
①パレート図
パレート図とは、項目ごとの数量を大きい順に並べた棒グラフと各項目の累積構成比を表す折れ線グラフで構成された複合グラフです。パレート図は、全項目のうちどの項目が全体に影響を与えている割合が大きいのかを明確にします。結果に対して影響が大きい要因に集中して対処することで、最小限の手間で大きな変化をもたらすことができます。
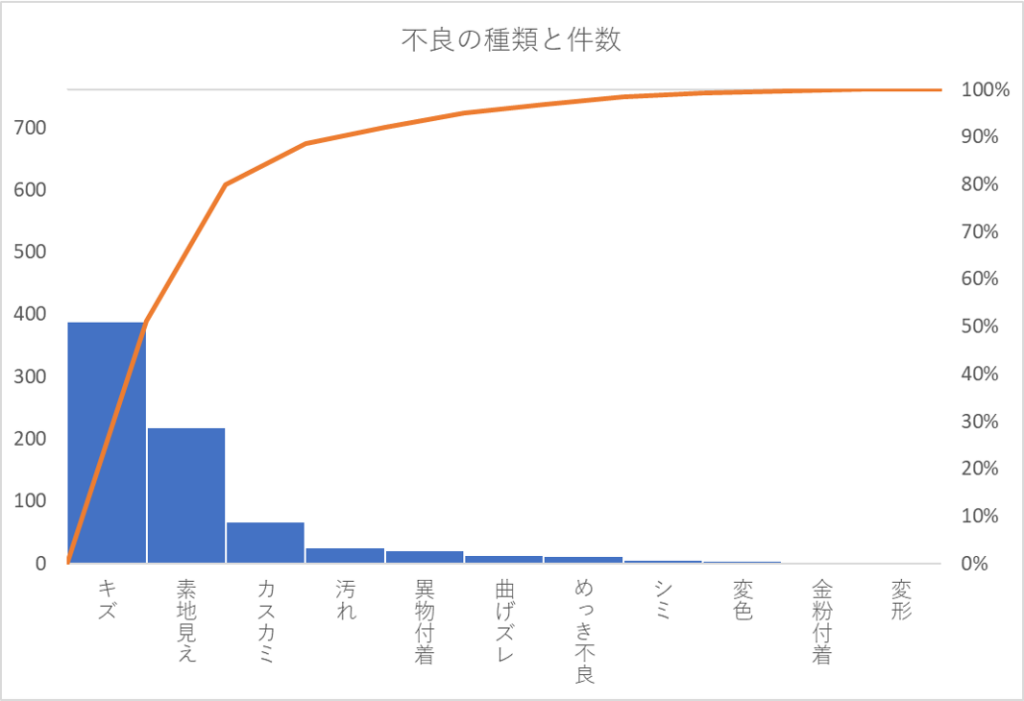
具体例
例えば、横軸にはキズ・素地見え・カスカミ・汚れ・異物付着・曲げズレ・めっき不良などの不良の種類、縦軸には各項目の不良品数を入れます。これにより、全体の不良に対してどの種類の不良が多いか一目で把握することができます。
どの不良が多いか把握した後、どの工程でその不良が発生しているか特定したいときにもパレート図が使用できます。横軸にはプレス・溶接・塗装・組み立て・検査など作業工程を、縦軸には各工程での不良品数を入れます。そうすることで重点的に対策すべき作業工程を洗い出すことができます。
注意点
パレート図はあくまで全体に対して割合の高い項目を把握するためのツールです。実際に問題解決に取り組むときには、パレート図が示す結果だけでなく、改善にかかる費用や時間などのコストも考慮して、その対策の実施が現実的に可能なのか判断しましょう。
②ヒストグラム
ヒストグラムとは、データが存在する範囲を一定ごとに区切り、区間ごとの数量を棒グラフで表したものです。横軸にデータが存在する範囲、縦軸には範囲ごとの数量が入ります。これによりデータのピーク値やばらつき具合、分布状況を一目で把握することができます。

具体例
例えば、横軸には製造に使用する電動ドライバーの圧力の数値が存在する範囲、縦軸にはその範囲に存在するデータの個数を入れることで、圧力のばらつき具合や規定の範囲を超えた数値の有無を一目で確認することができます。
注意点
ヒストグラムを作成するときは、適切な階級の幅(横軸の範囲)を設定する必要があります。階級の範囲が広すぎると多くのデータが同じ項目にカウントされてしまい、知りたい情報を把握できなくなります。逆に狭すぎるとデータが存在しない階級がでてくるなど、データのばらつきを確認しづらくなります。
③散布図
散布図とは、二つの特性を横軸と縦軸にとり、それぞれの数値が当てはまるところに点を打ったグラフです。これにより、二つのデータに関係があるのか無いのかが分かります。二つのデータにどのような関係があるのか見出すことで、問題を改善するための糸口を見つけられます。
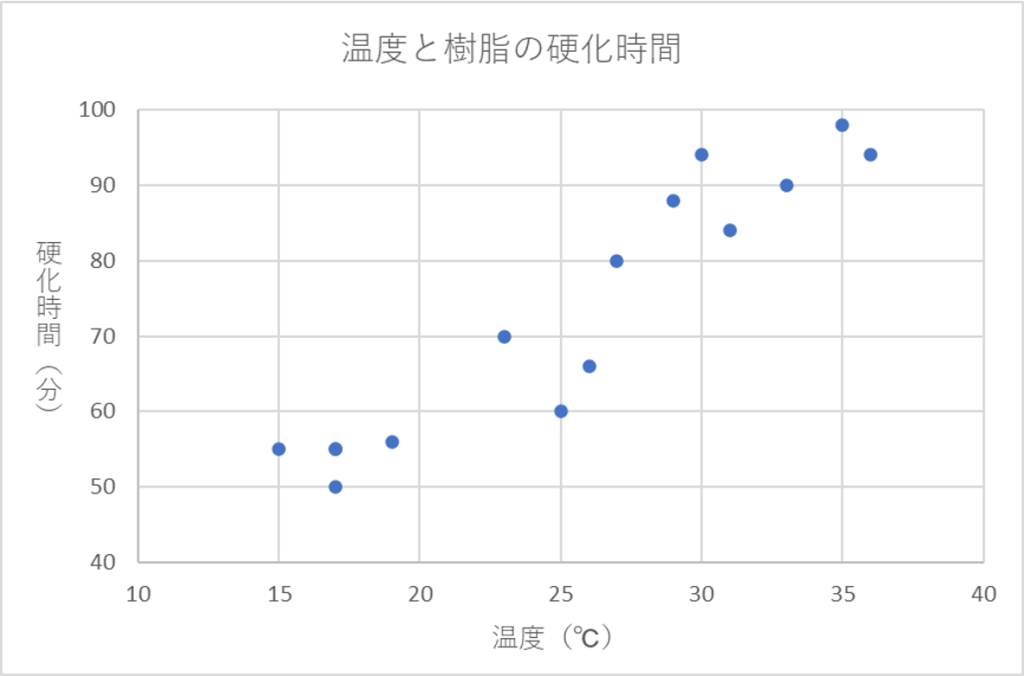
具体例
例えば、横軸に作業場所の温度、縦軸に樹脂の硬化時間を入れることで、作業場所の温度変化が樹脂の硬化時間に影響を与えている可能性があることが分かります。
散布状況は大きく以下の3種類に分けられ、それぞれの形状から読み取れる情報が違います。

注意点
散布図は、二つのデータに相関関係があるのかを把握するために使用されるもので、因果関係があることを証明するものではないので注意が必要です。相関関係とは2つの項目に何らかの関係があること、そして因果関係は二つの項目が原因と結果の関係にあることを示します。
④特性要因図
特性要因図とは、ある問題点(結果)について、影響を及ぼす原因(要因)を洗い出し、紐づけて表した図のことです。問題点と要因を洗い出す際には、ブレーン・ストーミングなどの手法を使って、少人数で意見を出し合い、さまざまな角度から深掘りしていきます。また、抽出された要因の図が魚の骨のようにみえることからフィッシュボーンチャートとも呼ばれます。
具体例
例えば、不良品増加という問題が起こった場合に、その原因となっている可能性がある事柄を洗い出すときに使用します。
要因を考えるとき、製造業における品質管理の4M(人、機械、方法、材料)を軸として考えると、図の作成時間を短縮できる上に漏れなく要因を洗い出せるため便利です。4Mについては以下の記事にまとめてありますので、ぜひ参考にしてください。
関連記事:4M変更とは?|製造業で欠かせない品質管理手法を紹介
⑤チェックシート
チェックシートとは、あらかじめ確認するべき項目や内容が記載されている記録用紙で、不具合発生を未然に防ぎ製品品質を担保するために使用されます。チェックシートを利用することで、効率的にデータを収集・整理することが可能です。チェックシートは使用目的によって形状や項目が様々ですが、大きく分けると点検用と調査用の2種類あります。
【点検用チェックシート】
点検用チェックシートは、主に点検項目の抜けや忘れを防ぐために使用されます。また、チェックシートを見るだけで誰でも素早く点検する内容を理解できるため効率的に作業を行えます。
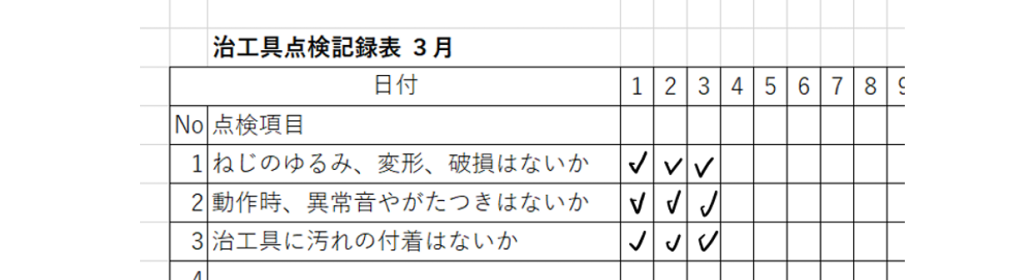
具体的な使用シーンとしては、製造に使用する治工具や機械の点検・検査時や温度・湿度など作業環境が定められた基準を満たしているのか確認するときに使用されます。
使用にあたっての注意点ですが、ただ用紙にチェックを付けるという作業にならないようにしなければなりません。点検する意味や目的を作業者に伝え、責任を持って作業を行ってもらう事が重要です。
【調査(記録)用チェックシート】
調査用チェックシートは、データを収集し分析に活用することが目的です。調査用チェックシートに記録したデータを、グラフに当てはめて分析するなどして、集めたデータを活用できます。また、調査用チェックシートを見ただけで問題点がどこにあるのか分かるように設計することで、記録後にそのまま分析に用いることもできます。
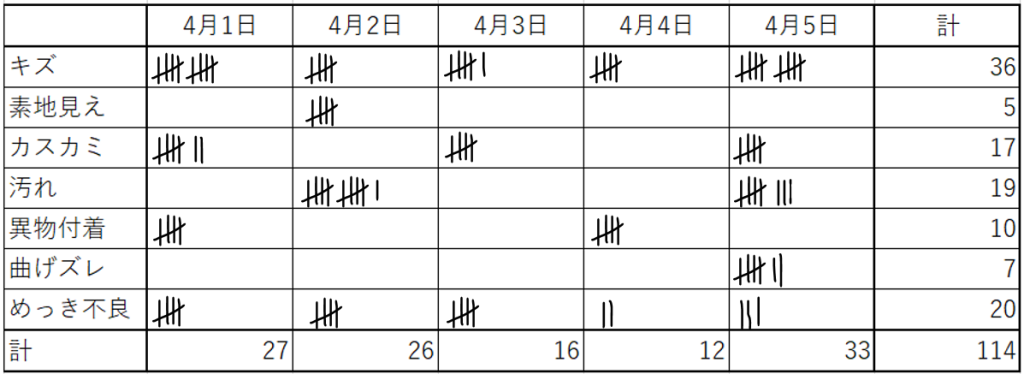
具体的な使用シーンとしては、不良品数を記録することで、どのような種類の不良がどのくらいの量あったのかを関係者に報告したり、不良品削減のための改善活動を考えるときに活用されます。
チェックシートを設計するときには、使用目的を明確にし、あらかじめ目的を達成するために必要なデータを収集できるように項目を設ける必要があります。
⑥グラフ
グラフは2つ以上のデータの関係性を図表化し、視覚的に全体像を把握または比較しやすくするために用いられます。グラフには様々な種類があり、これまでに紹介したパレート図やヒストグラム、散布図などもグラフの一種です。ここでは分析によく用いられる代表的な4つのグラフの特徴と製造業での具体的な使用シーンについてまとめています。
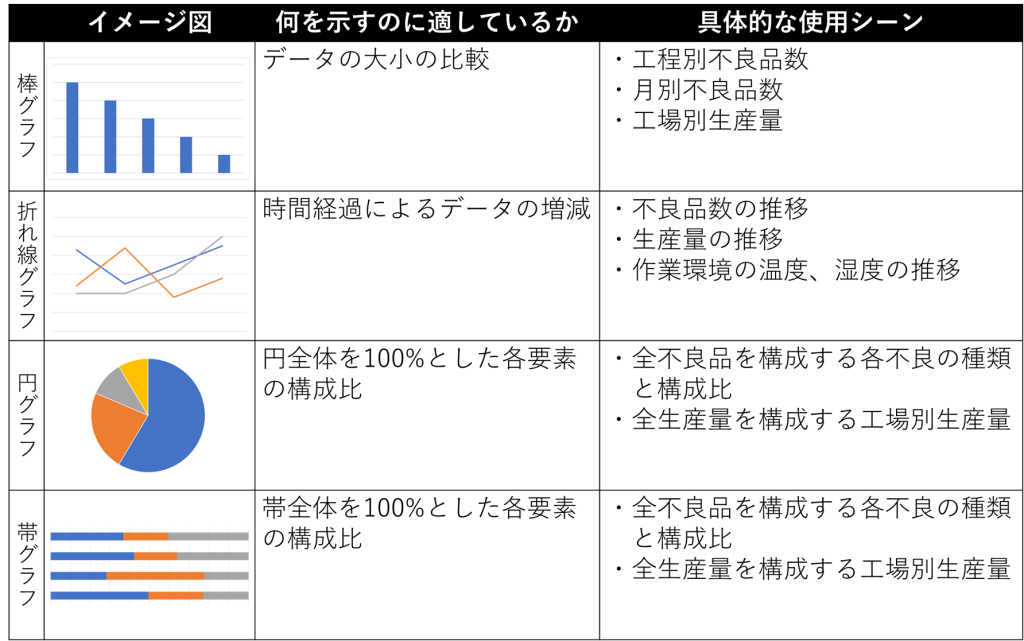
グラフを使用するときには、何を知りたいのかという目的を明確にし、その目的を達成するために最適なグラフはどれなのか考えて使用するグラフを選びましょう。
⑦管理図
管理図とは、工程上での品質のばらつきが、偶然起こったものなのか、それとも何らかの異常によって起こったものなのか判断するために使用されます。中心線(CL)・上方管理限界線(UCL)・下方管理限界線(LCL)の3つの要素から構成されており、取得したデータは折れ線グラフで表されます。上方管理限界線と下方管理限界線の間にデータが存在していれば正常、はみ出していれば異常というように視覚的に判断することができます。
具体例
管理図は作業工程が正常に管理されていることを確認するためや、安定状態を維持するために使用されます。例えば、横軸にはサンプリングを行った日付、縦軸には製品の強度や反り具合など品質にかかわるデータを入れます。そうすることで品質の変化がどのタイミングで起こっているのか把握できます。また、管理限界を超えるアウト(管理外れ)があることを確認できれば、正常な状態に修正するための対策につなげることができます。
注意点
管理限界は、データがその範囲を超えたときに対策を実行する、というアクションを起こすタイミングの目安として設定します。そのため、管理限界の範囲が狭すぎるとアクションを起こす回数が増える分労力がかかり、広すぎると不具合の発生を見落とす可能性が高くなります。この2点を考慮し、自社の規模に合わせて限界線を設定する必要があります。
3. まとめ
本記事ではQC7つ道具を使用する目的や、それぞれの使い方、どういう状況で使用すれば有効活用できるのかについて説明しました。ぜひ本記事を参考に現場での問題解決や品質維持、改善活動にお役立てください。
弊社では、ISO9001を取得し、お客様に対して、安定した品質レベルの製造請負サービスを提供できるよう、迅速な初期対応、安定した品質管理、徹底した納期遵守・適材適所の配置を強みに請負サービスの拡大に努めております。HPに記載されていない案件でも誠意をもって対応させて頂きますので、まずはお気軽にお問い合わせください。