4M変更とは?|製造業で欠かせない品質管理手法を紹介
投稿日:2022/2/26
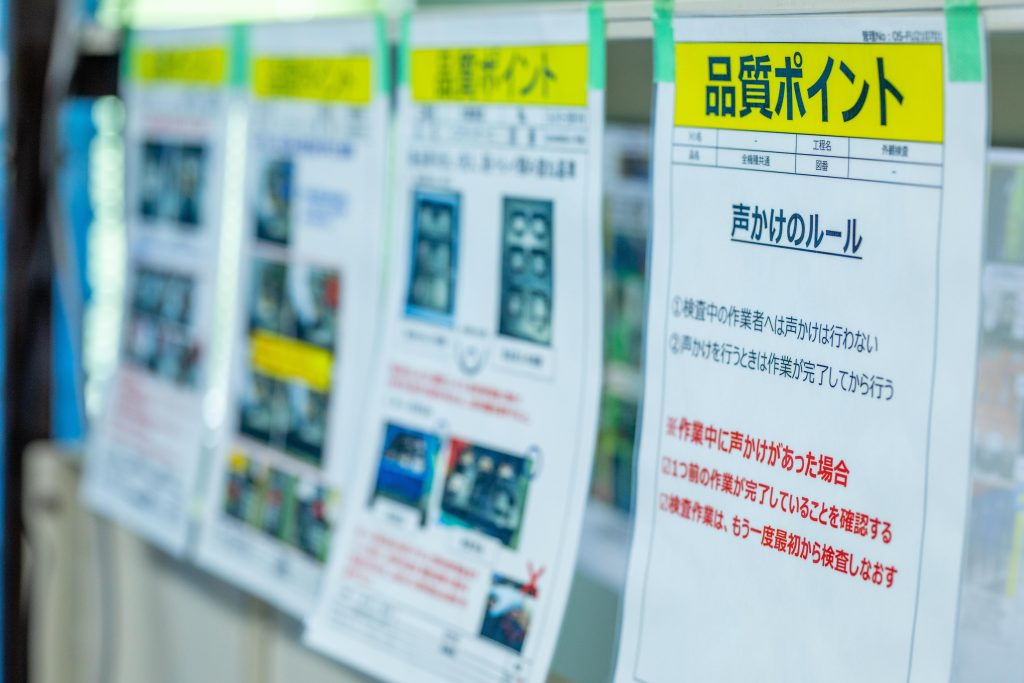
製造業において品質管理は製品だけでなくブランド全体の信用を保ち、顧客満足度を高めたりクレームを減らしたりするためにとても重要です。この記事では、品質を適切に管理するための「4M変更」という方法を紹介します。製品の品質管理を担っている方や4M変更管理の導入方法を知りたい方向けに以下について述べています。
- 4M変更の目的
- 4M変更を導入した方が良い理由
- 4Mで発生する問題と解決策
- 4M変更以外の品質管理手法
本記事をご覧いただくことで、「既存の品質レベルを改善するにはどうしたらいいのか」「4M変更を基に改善点を見つけるにはどうすればいいか」がお分かりいただけます。
1. 4M変更とは
4M変更とは4M変化点とも呼ばれ、製造業における製品の品質管理手法の一つです。製造現場をMan(人)、Machine(機械)、Method(方法)、Material(材料)の4つの観点から、それぞれの変化点を事前に把握し、その変化点で生じやすい品質トラブルを未然に防ぐ方法です。
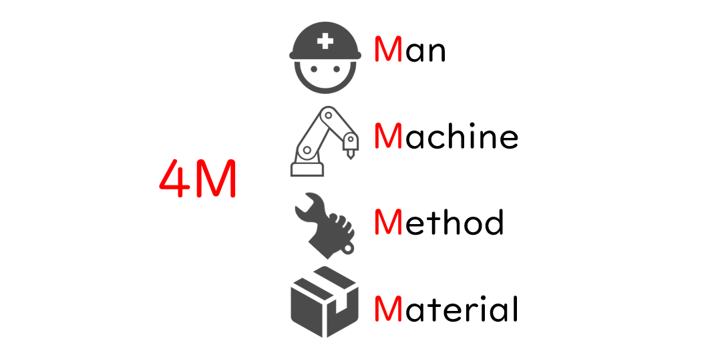
1.1 4M変更を行う目的
4M変更の目的は、
- 製造業で起きやすい3つのトラブルの予防
- 問題発生時の原因究明
の2点に分類されます。
製造業で起きやすい3つのトラブルの予防
一つ目は、安全トラブルです。製造現場には下記のような危険が潜んでいます。
- 機械の操作ミス・危険場所への侵入といった作業員の不注意
- 作業着、手袋、安全靴の不適切な着用
- 機械の誤作動
- 人体へ悪影響を及ぼす危険性のある薬品の使用
上記のようなトラブルを防ぐためには、安全で誰にでも分かりやすい作業マニュアルの用意や製造現場のレイアウトを考えるなど危険を排除するための対策を行う必要があります。
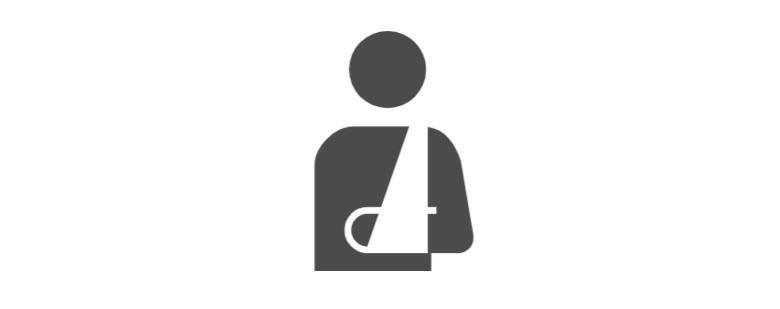
二つ目は、設備トラブルです。長期間にわたり同じ設備を使い続けると下記のようなトラブルが発生しがちです。
- ねじの緩み
- パーツの欠け
- 劣化
- ゆがみ
機械が正常に動作しなければ不適合品の流出増加や従業員のケガにもつながります。こういった事故を起こさないためにも、普段から機械の使用方法を守りメンテナンスや点検を怠らないことが大切です。
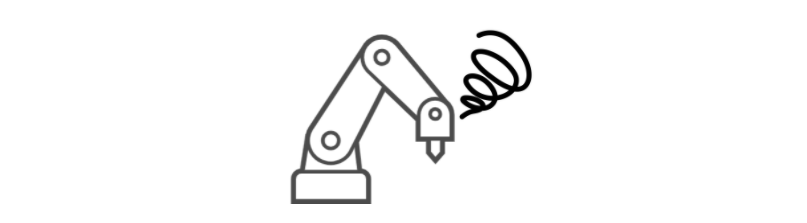
三つ目は、在庫トラブルです。在庫の管理を怠ることで、下記のようなリスクがあります。
- 材料欠品
- 余剰在庫
- 材料の劣化
- 材料の廃棄
例えば、入庫日時が古い材料から順番に製造工程に流す先入れ先出しという在庫管理方法があります。これは長期滞在による材料の品質低下を防ぐために行われます。この先入れ先出しが適切に行われていないと、廃棄材料・廃棄コストの増加というトラブルを引き起こします。
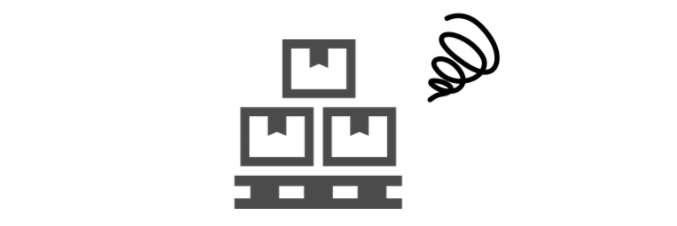
問題発生時の原因究明
4M変更によって、問題発生時に製造工程を振り返って原因を素早く特定することができます。そのため、想定外の問題でも適切に対処することができます。例えば不適合品が流出した場合、製造工程を振り返りながら、以下のような原因を考えることができます。
- 作業員のスキル不足、経験不足、注意不足による作業ミス
- 機械の不具合、故障
- 機械の使用方法、点検方法の誤り
- 作業方法の誤り
- 作業方法の伝達ミス
- 材料の保管方法の誤り
このような変化点管理をしていないと、トラブルが発生した際にその問題の波及範囲を特定することができず、お客様との信用問題になりかねません。
2. 4Mが変化するタイミング
この章では4Mが変化する状況と変化によって起きがちな問題を説明します。下記のような変化点を事前に把握しておくことで問題発生の予防や原因究明に活用できます。
2.1 Man (人)の変化
スタッフの新規雇用・退職
新しいスタッフを採用したとき、またはスタッフが退職したときに人の移動が起こります。スタッフが退職し欠員補充したときに品質トラブルが発生しがちです。作業に慣れていないスタッフが作業を行うため、スキルや知識不足・経験不足による作業ミスが発生する可能性が高いです。
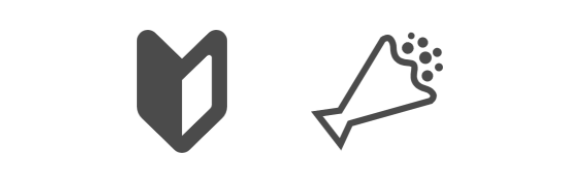
スタッフの配置変え
担当する作業に対して適性のないスタッフが作業を行った場合、品質トラブルが発生する可能性が高くなります。例えば、高齢化によって作業スタッフの視力が低下していた場合、精密な部品を目視する必要がある作業を行うと見落としミスが発生する危険があります。そのため、製造現場ではスタッフのスキルや経験・特性に応じて適性を把握し、時と場合に応じて担当させる作業を決定、変更することが重要です。
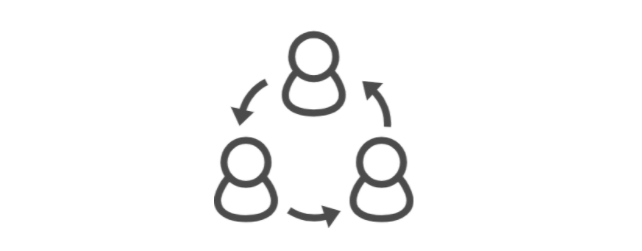
シフト勤務
シフト勤務とは休みなく現場を稼働させ続けるために一定の時間で作業員を交代させる勤務体制です。このように労働者が入れ替わるときに人が変化するので問題が発生しやすいです。例えば、前半グループで起こったトラブルや注意点等の情報を後半グループに伝え忘れるケースが考えられます。
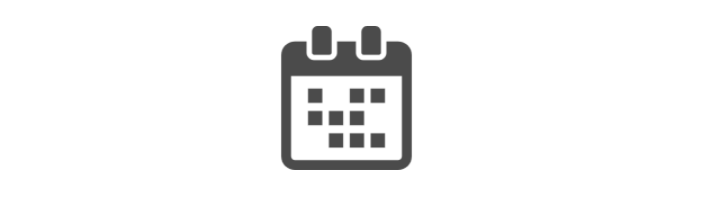
2.2 Machine(機械)の変化
機械設備の導入・金型の変更
機械の操作方法や機械自体が変更されると作業者が注意する点も変わります。特に以下のタイミングでミスが発生しやすくなります。
- 新製品の製造
- 機械パーツの一部の変更
- 製造する製品の形状・デザインの変更
これらの変化点を作業員が正しく把握できていない場合、製品の品質が低下するリスクが高まり、さらには誤使用による機械の故障や作業員の怪我につながります。
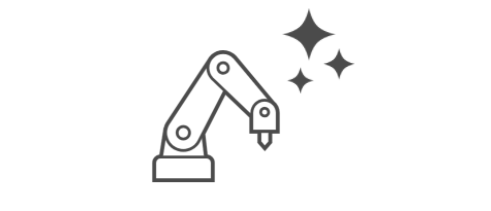
また、機械設備の導入後に製造する初回ロットは、不適合品が発生しがちです。下記のような理由で不適合品が製造される可能性があります。
- 使用する金型に問題がある
- 金型の取り付けが不十分である
- 作業方法が不適切である
廃棄ロスを削減するために少量から製造を始め、改善点や異常の有無を検査し問題がないことを確認してから量産を始めましょう。
治具の設定変更
同じ治具を使用して違う製品を製造する時、作る製品によって治具の設定変更を行います。以下のような状況でミスが発生しやすくなります。
- 電動ドライバーの圧の変更
- プレス機のエアー圧の変更
適切に治具の設定変更が行われていない場合、製品の完成具合にバラつきが生じ品質低下を招きます。
ルールの理解不足と不徹底
点検方法が定められていても、作業者起因によるヒューマンエラーも考えられます。例として以下のような状況が挙げられます。
- 理解不足による誤った点検の実施
- 不適切な点検の実施
このように、点検方法が作業者の理解不足や不徹底によって変更されることで、機械の不具合を発見できず、機械の故障や不適合品の流出に繋がります。
2.3 Method(方法)の変化
作業方法の変更
生産性向上のために作業方法が変わることがあります。この時、変更内容が作業スタッフ全員に正しく伝達されていないという問題が発生する可能性があります。正しい作業方法を行わずに製造を行うと作業効率の低下や不適合品の流出に繋がります。
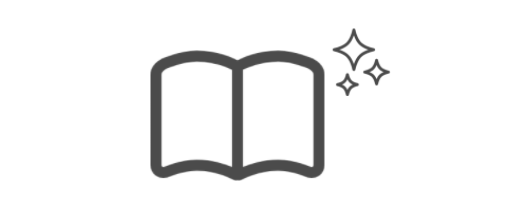
作業場所の変更
下記の理由で従来の製品の作業場所が変更される場合があります。
- 生産ライン拡大に伴う作業場所の変更
- 工場全体のレイアウトの見直し
作業場所が変更されると以下のような変化が生じ、ミスが発生しやすくなります。
- 温度や湿度などの作業環境の変更
- 作業台や機械のレイアウトの変更
製品によっては作業環境の変化による悪影響を受けるものもあります。また、レイアウトの変更は作業効率へ影響するため、適切な配置を考えないと生産性の低下に繋がります。
2.4 Material(材料)の変化
材料・材質の変更
以前まで使用していた材料が入手困難になると、使用する材料や材質が変わります。以下のような変化点でミスが発生しやすくなります。
- 材料の入手ルートの変更
- 材料仕入れメーカーの変更
同じ名前の材料でも原産地や製造工場が変わった場合、従来使用していた材料と比べてわずかに分量が違っていることがあります。材料の変化は製品へ直接影響するため、品質の低下を招きます。
材料の管理方法の変更
材料の管理方法の変更に伴って、以下のような保管環境も変化します。
- 温度
- 湿度
- 場所
使用する材料によっては変化の影響を受けやすいものがあります。影響を受けた材料を使用して製品を製造した場合、製品の品質低下に繋がります。
3. 4Mで発生しがちな問題への解決策
前章では4Mの変化点によって発生しがちな問題を紹介しました。これらを把握しておけば、事前に対策を立てることが出来ます。この章では、4M変更管理を製造現場へ導入し、発生しがちな問題の解決策についてお伝えします。
3.1 Man(人)
新人教育

研修生が作業を行った製品にはタグ付け
- →タグが付いている製品を習熟したスタッフがこまめに点検
- →不適合品の流出を防止
研修生の腕章
- →研修生であることを周知
- →周りのスタッフによるサポートが容易に
このような方法で新人教育体勢を整える事で、人の変化による品質のバラつきを抑制することができます。
作業員のスキルを審査
技能認定試験の実施
- 1.作業するために必要な能力やスキルを審査
- 2.審査に合格した人を作業員に認定
- 3.定期的な審査を行い作業員の能力低下に対応
→長期的な品質の維持が可能に
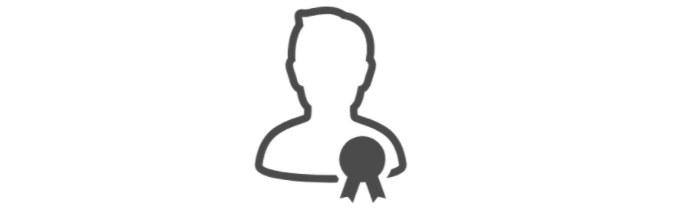
シフト交代時の引継ぎ
業務引継書
- 業務の進捗状況、業務中のトラブル・注意点、改善した更新点などを記録
- フォーマット化することで引き継ぐ情報の抜けや漏れを防止
- 1.引き継ぐべき内容の洗い出し
- 2.引継ぎ内容を後任者に分かりやすいように記載
- 3.後任者が引継書を確認
→伝達ミスを防止
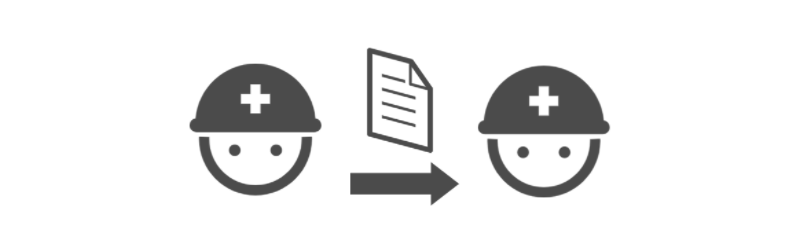
3.2 Machine(機械)
機械メンテナンス
日常点検簿
- 点検箇所・内容・日時などを記録
- 機械によっては稼働前・中・後で確認項目を分けて点検
- 1.作業者が点検簿の項目を確認しながら点検
- 2.現場リーダーが点検内容と点検簿を確認
- 3.適切に点検が行われていたら確認欄に押印
→機械の不具合を未然に防止
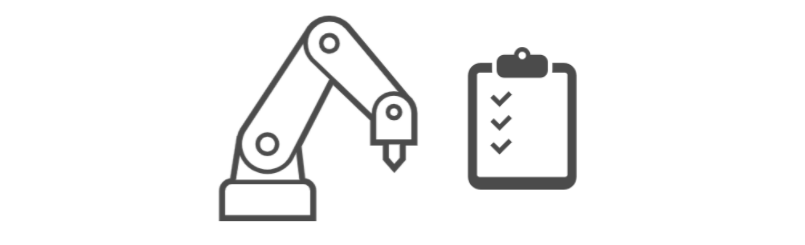
点検簿を運用する時は、点検簿にただチェックを付けるという作業にならないようにしなければなりません。点検する意味や目的を作業者に伝え、責任を持って作業を行ってもらう事が重要です。そして、現場リーダーも作業者が適切な点検を行っているか、定期的な確認作業も大切です。
3.3 Method(方法)
作業方法の指導
作業指導記録表
指導した日時、内容、指導者、指導対象者、指導期間を記録
- 1.指導者が実演しながら作業方法を説明
- 2.対象者の作業を指導
- 3.製品と作業内容の出来栄えを現場リーダーが判定
- 4.教育効果があれば記録表に押印
- 5.慣れたころに逆指導させ、出来栄えを確認(作業者→現場リーダーへ)
- →誤った作業方法の伝達を防止
- →作業方法の統一
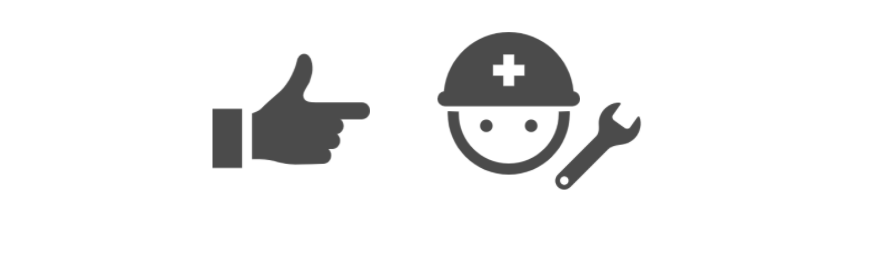
分かりやすい作業手順
作業手順書の作成
- 文章だけでなく図や写真を用いた説明
- 注意点やミスを記載
- 作業の正常な状態と誤っている状態の写真を設け比較可能に
→誰が見てもわかりやすい作業手順書に
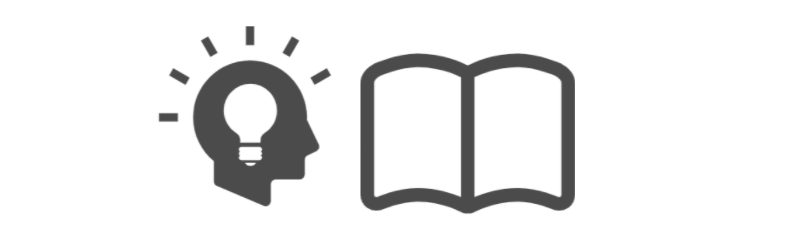
品質ポイントの明確化
注意点の張り出し
- 1.過去に起こったトラブルの洗い出し
- 2.トラブルの内容や注意点を文章や写真を用いて紙媒体に
- 3.作業者の目につく場所へ張り出し
- →作業者が注意点を容易に把握可能
- →作業初心者への説明が簡単
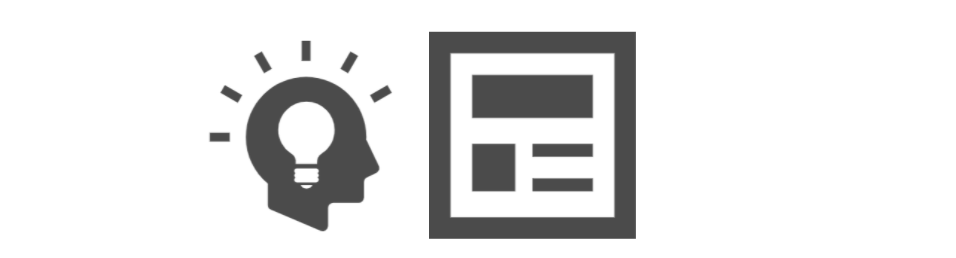
3.4 Material(材料)
材料管理
材料管理表
取り扱う材料に応じて必要な管理条件を記録(例:温度・湿度・気圧・開封日時・使用期限など)
- 1.作業者が管理表の項目を現物を見て確認し記入する
- 2.現場リーダーが管理表を確認
- 3.問題がなければ確認欄に押印
→材料が適切に管理されているか把握可能
4. 4M変更管理をさらに発展させた品質管理手法
4M変更管理では製造における管理を4つの要素に分けて変更の記録を行います。しかし従来の4つの要素の管理だけでは品質管理手法として不十分であるという考えのもと、考案された「5M+1E」・「6M」と呼ばれる品質管理手法があります。「5M+1E」とは、4MにMeasurement(測定)とEnvironment(環境)を追加したものです。そして、「6M」とは、上記の5MにManagement(管理方法)を追加した品質管理手法です。既存の品質レベルに対して、目標としている品質レベルを達成するため、管理部門と現場が、無理のない運用可能なレベルの品質管理を導入することもとても大切です。無理に導入しようとしても、管理が煩雑になり、形骸化してしまっては意味がありません。
5. まとめ
本記事では4M変更を行う目的、そして4Mの変化点で生じやすいトラブルとその解決策についてご説明しました。また、4M変更を現場へ導入するポイントと管理方法について解説しました。これから社内や外注先で品質強化に取り組まれる方にとって役立つ記事となっていれば幸いです。
弊社では、ISO9001を取得し、お客様に対して、安定した品質レベルの製造請負サービスを提供できるよう、迅速な初期対応、安定した品質管理、徹底した納期遵守・適材適所の配置を強みに請負サービスの拡大に努めております。HPに記載されていない案件でも誠意をもって対応させて頂きますので、まずはお気軽にお問い合わせください。