員数管理とは?目的や方法、よくあるミスへの対策を説明!
投稿日:2023/5/12
皆さんは員数管理(読み:いんずうかんり、いんすうかんり)という言葉を聞いたことがありますか?員数管理とは、員数に過不足がないか確認する作業です。例えば、1つの製品を作るために必要な部品の数がそろっているか確認する作業を員数管理と言います。
この記事では、そんな員数管理について、目的や員数管理を行うタイミング、方法について簡単に説明しています。
なお、当社では員数管理をはじめとした品質管理を徹底し、創業以来50年以上にわたりお客様へ安定したサービスを提供しています。現場の知識や経験がベースとなっているため、ぜひ参考にしてください。
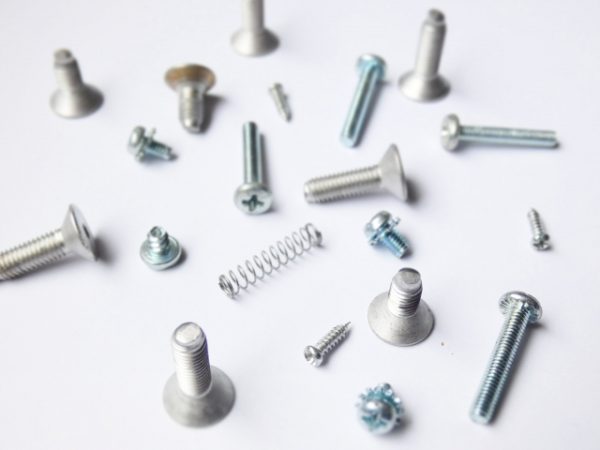
1. 員数管理とは?
員数とは「枠内にある人やモノの数」を意味します。特に、製造業では「1つの製品を作るために必要な部品の個数」という意味で使用されます。
員数管理(読み:いんずうかんり、いんすうかんり)とは、員数に過不足がないか確認する作業を指します。例えば、1つの製品を作るために必要な部品の数がそろっているか確認する作業を員数管理と言います。
企業によっては「員数チェック・員数検査・員数検品・検数・員数確認」と呼ばれることもあります。
2. 員数管理の目的は?
製造業における員数管理の目的は、入荷数や製品数、出荷数などの数量が合っているか確認し、数え間違いによって発生するミスを予防することです。
2.1. 員数管理を行うタイミングは入荷時・製造時・出荷時
員数管理を行うタイミングは、主に入荷時、製造時、出荷時の3つです。
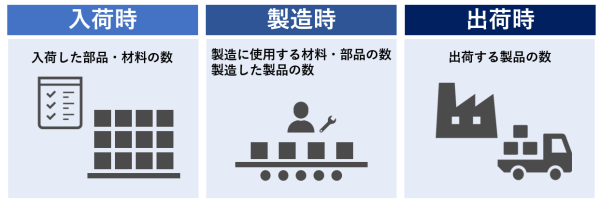
入荷時
注文した数と実際に入荷した部品・材料の数が一致しているか確認します。
製造時
製造を始める前に、あらかじめ必要な部品や材料の数を確認します。また、製造した製品の数が計画と一致しているか確認します。
出荷時
注文された数と実際に出荷する数が一致するか確認します。
2.2. 員数管理で防げるミス
員数管理を適切に行えば、以下のようなミスを防ぐことができます。
入荷時のミス
- 注文した数より実際の入荷数が少なく、製品の製造に必要な材料がない
- 注文した数より実際の入荷数が多く、在庫スペースを圧迫している
製造時のミス
- ネジの締め忘れがあった
- 部品の取り付け忘れがあった
- 製品を多く作りすぎた
出荷時のミス
- 注文された数と実際の出荷数が間違っていた
このようなミスを防ぐために、効率良く正確に員数管理を行いましょう。
3. 員数管理の方法を5つ紹介
適切な員数管理の方法は、数えたい対象物のサイズや重さ、特性、製造方法などによって変わります。ここでは、代表的な手法を5つ紹介します。メリット・デメリットについてもまとめたので、ぜひご活用ください。
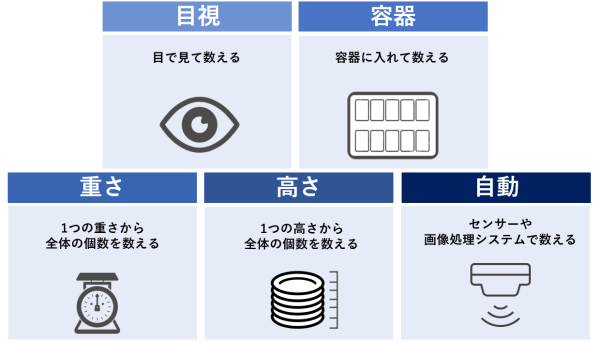
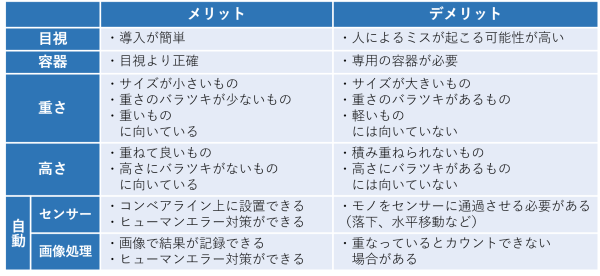
それぞれの方法について詳しく説明します。
3.1. 目視確認
目視確認とは、人の目で見て個数を確認する方法です。

簡単に導入できますが、ヒューマンエラーが起こりやすいという難点があります。そのため、以下の方法をいくつか組み合わせることでミスを減らせます。
- 声に出して数える
- 指さしで数える
- 数取り器などの道具を使用して数える
- チェック用紙に記入しながら数える
- スマートフォンやタブレット端末のチェック項目に記入しながら数える
3.2. 容器計測
容器計測とは、専用の容器を使って数を確認する方法です。
例えば、製品が10個入る専用トレーを用意して、入れながら数字を数えます。専用の容器を用意する手間はかかりますが、抜けがあれば一目でわかるので目視確認より正確でしょう。
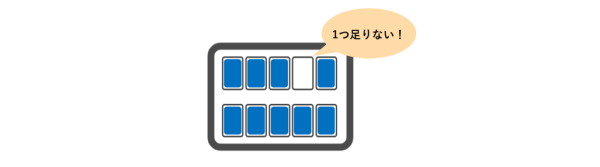
「員数管理 トレー」で検索すると様々な種類が出てきます。適切なものが見あたらない場合は、オーダーメイドでの依頼も可能です。
3.3. 重さ計測
製品単体の重さと全体の重さを比べ、全体の個数を把握する方法です。
カウンティングスケール(個数はかり)という測定器を使用すれば、素早く正確に個数をカウントできます。重量や個数の表示だけでなく、バラツキ補正機能やラベルの印字機能、計測履歴の保存機能等が付いているものもあります。使用時には校正や点検を怠らないようにしましょう。
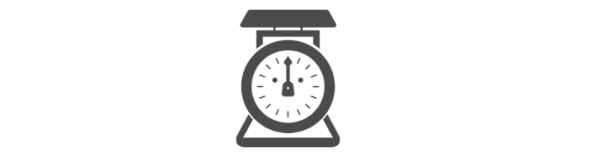
重さ計測は、サイズが小さく、重さにバラツキが少ないもの(ネジや部品等)を数える時には便利な方法です。しかし、サイズが大きく重さにバラツキがあるものは向いていません。
3.4. 高さ計測
高さ計測とは、製品単体の高さと積み重ねた高さを計算し、全体の個数を把握する方法です。メジャーやハイトゲージという道具を使用すれば、正確な高さを図ることができます。
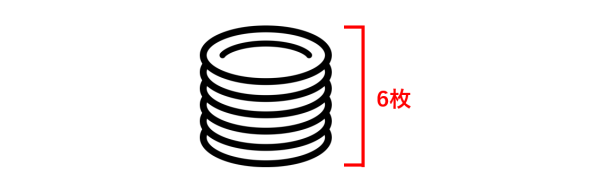
ただし、高さにバラツキがある製品や重ねてはいけない製品を数える方法としては向いていません。また、高さのバラツキを考慮するのは難しいため、正確性は低いと言われています。他の方法と組み合わせ、ダブルチェックとしての使用がおすすめです。
3.5. 自動計測
自動計測とは、センサーや画像処理システムを利用して、自動で個数を数える方法です。人が関与しないため、ヒューマンエラーを防止できます。
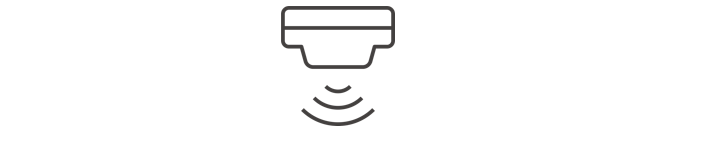
センサーを使用する場合は、対象物にセンサーを通過(落下や平行移動)させてカウントします。例えば、コンベアラインで製造を行っている場合、ライン上にセンサーを設置すると自動で数えられます。
画像処理システムを用いて数える場合、専用の機械を使用します。計測台の上に対象物を広げ、カメラが撮影し、画像処理システムによって個数を数えます。作業記録を残せるものもあり、振り返って確認することができます。
4. 員数管理で良くあるミスと対策方法
前章では、員数管理を行う方法を紹介しました。しかし、これらの方法を用いても、ミスが発生してしまうことがあります。この章では、員数管理を行うときに発生しやすいミスと、発生を防止する方法について説明します。
4.1. 員数管理で発生しやすいミス
員数管理で発生しやすいミスは主に「人によるミス」と「作業環境によるミス」の2つに分類できます。
人によるミス
員数管理は人が行うことが多いため、人間が原因となって起こるミス=「ヒューマンエラー」が発生しがちです。ヒューマンエラーには、作業者本人に自覚がない状態で発生するミスと、作業者本人に自覚がある状態で発生するミスの2つに分類できます。
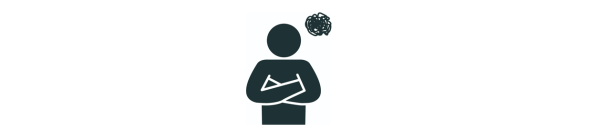
例えば、日付の記入ミスや治具の日常点検忘れなどは、知識や経験不足、連携不足、勘違い、疲労による集中力の低下等が原因で本人の意図とは関係なく発生します。
面倒で工程を飛ばしたり、作業時間を短縮するために確認をしなかったというミスは、作業者が意図的にしているミスです。手抜きやマニュアル手順の無視が原因で発生します。
このように、人間が作業を行うと、どうしてもミスが発生してしまいます。
作業環境によるミス
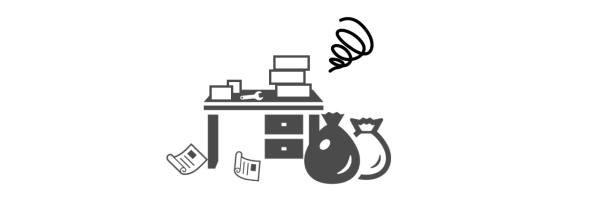
また、作業環境が原因でミスが発生するパターンもあります。
例えば、次のような5S(整理、整頓、清潔、清掃、しつけ)が出来ていない作業環境では、ミスが発生しやすいです。
- 整理整頓されていない
- どこに何が置いてあるか分からない
- 道具をしまう定位置が決まっていない
- 定められた位置に道具がしまわれておらず、作業台に置きっぱなしになっている
- 在庫保管場所の位置が悪く、他製品の置き場と間違えやすい
作業環境の悪化は、生産性の低下や作業者のモチベーション低下に繋がってしまいます。また、ヒューマンエラーの原因にもなるため、作業環境を整えることは企業と従業員双方にとって大切です。
職場の環境改善ができる「5S活動」については、下記リンクからどうぞ。
関連記事:5S活動とは?意味や効果・進め方やアイデア事例を紹介
4.2. ミスへの対策方法
前章では、員数管理でよくあるミスを2つ紹介しました。ミスを完全に無くすことは難しいですが、1度起きてしまったミスを繰り返さないために再発防止策を考えることで次につなげましょう。この章では「なぜなぜ分析」を使用したミスの再発防止策の手順を紹介します。
①問題を明確にする
まずは、問題を明確にしましょう。問題が明確でないとこれから探っていく原因も曖昧になり、根本的な問題解決に繋がりません。「やってしまった、悪い」などの曖昧な表現ではなく「出荷した製品Aの箱に製品Bが混入していた」のように事実を具体的に表すようにします。
②なぜなぜ分析で真因まで分析
なぜなぜ分析とは、1つの問題に対して「なぜ?」という質問を5回繰り返すことで、問題の原因を特定する方法です。一般的に「なぜ?」を5回繰り返すことで、問題の真因にたどり着くことができると言われています。
- 例)「出荷した製品Aの箱に製品Bが混入していた」
- 1. なぜ? 作業員が製品Aと製品Bの置き場所を間違えたから
- 2. なぜ? 製品Aと製品Bの置き場所が紛らわしいから
- 3. なぜ? 製品A置き場と製品B置き場の場所が近いから
- 4. なぜ? 他に空きスペースが無かった
- 5. なぜ? 作業場レイアウトが適切ではなかった
なぜなぜ分析のポイントは、原因をヒューマンエラーや個人のせいにするのではなく、仕組や体制まで落とし込むことです。「作業員の不注意」と人のせいにするのは簡単ですが、対策を考えるときに「注意するように心がける」のような曖昧な表現になってしまいます。具体的で効果のある対策を行うために、仕組みや体制に真因を見つけましょう。
➂ルールを見直し、周知する
原因を仕組みレベルまで落とし込んだ後は、ルールを見直し周知しましょう。
例えば、作業場所のレイアウトを変更し「製品が混ざらないように離れた場所に置き場所決め、テープで分かりやすいように囲む」というルールに修正します。
そして、変更後は変更内容の大小にかかわらず作業者全員に周知することが重要です。作業者全員に変更内容が伝わっていないと、同じミスを繰り返してしまう可能性があります。伝達後は、きちんと修正された内容を守っているか確認を行うことで、ミスを低減できます。
5. まとめ
この記事では、員数管理の概要や管理方法、よくあるミスと対策について説明しました。員数管理について知りたい方や、職場での員数管理ミスを抑えたい方にとって役立つ記事となっていれば幸いです。
当社では、継続的な品質管理や現場改善に取り組み、お客様に安心していただけるサービスの提供を心掛けています。HPに記載されていない案件でも誠意をもって対応させて頂きますので、まずはお気軽にお問い合わせください。